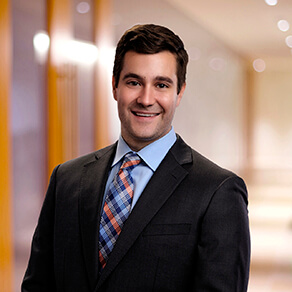
Common Construction Accounting Risks and How They Can Be Prevented
The construction industry has experienced a significant amount of growth post-pandemic. While increased job activity is a positive, several risks have become more prevalent, which could negatively impact job performance if overlooked.
Implementing efficient accounting practices can prevent companies from experiencing deteriorating margins and assist in mitigating the following common risks, helping companies gain a stronger understanding of bidding processes and projected job performance.
1. Inaccurate Cost Estimates: With numerous jobs available for bid, construction industry experts face a rising risk of inaccurate cost forecasts. Poor estimates lead to underbidding and cost overruns. Contractors should use detailed, line-item estimates for each job site activity, including labor, materials and equipment hours. These costs should be continuously evaluated and adjusted as the project progresses and work scopes change. Regular evaluation of estimates and comparison of budgeted to actual costs enables accurate forecasting of the job’s trending performance and helps refine estimates in future projects.
2. Overhead Overlook: Overhead costs are a notable expense in the construction industry. Fixed overhead costs, such as office rent or insurance, are straightforward to account for, whereas variable overhead costs, such as labor burden, repairs and maintenance, and advertising, can fluctuate and be easily overlooked. Common pitfalls include not considering indirect costs and overhead during the bidding process and not allocating these costs to the work-in-process schedules on a timely basis when evaluating a job’s performance. To prevent overhead overlook, companies should utilize a variety of formulas to allocate indirect costs and overhead. Allocation formulas most commonly used include, but are not limited to:
-
- Allocate indirect costs and overhead based on direct labor;
- Allocate indirect costs and overhead based on material costs; and
- Allocate indirect costs and overhead based on equipment use.
Tracking construction project costs is already time-consuming without factoring in overhead and direct costs. However, it is crucial for companies to understand and track the difference between direct, indirect and overhead costs on each job, starting from the bidding stage and on a continuing basis as projects progress.
3. Increased Market Prices: Post-pandemic, the construction industry has faced extreme cost volatility. Since 2020, average hourly wages have risen approximately 17%, and overall construction input costs have surged by 40.7%. Costs throughout the industry are expected to continue increasing for the foreseeable future, requiring companies to take into consideration and adjust their budget and bidding processes accordingly. They can even look for other avenues to help mitigate inflationary costs, including:
-
- Requesting deposits to purchase and store materials before construction of a project begins.
- Incorporating percentage change clauses in contract agreements that allow cost overruns from price increases to be billed back to the project’s owner.
4. Cash-Flow Overruns: Rising costs can also lead to cash flow shortages, which can create materials and equipment delays. When materials and equipment have delayed deliveries, companies may need to postpone projects, which can have various negative impacts. To prevent this, companies should establish strong budgeting and accounting estimates of cash flows. Estimating when certain milestones will be met will help you develop and track a proposed payment schedule and provide a good idea of how cash inflow will correlate with cash outflow on jobs.
5. Out-of-Scope Work: It is inevitable that construction projects will face unexpected changes, such as poor weather, last-minute changes, punch list items and job add-ons. It is essential to consider and account for out-of-scope work during the bidding process and when forecasting the project’s expenses and performance. Project managers should maintain open communication with the accounting department to continuously compare actual costs with estimates throughout the life of the project. Identifying lower-than-expected margins early provides management time and justification to refuse extra work or work with the project’s owner to find a suitable middle ground.
Having strong accounting procedures and controls, such as budgeting, tracking job performance, accurate cost allocation, cash flow projection, and many more, helps mitigate these risks and their negative impact on job performance and a company’s bottom line. Paying attention to the numbers and prioritizing the accounting and financial aspects of jobs can be a crucial factor in increasing margins and advancing your company’s success.
Contributing author: Robert C. Reeves, CPA, CFE, is an audit partner with over eight years of experience at the firm providing audit, review, compilation and consulting services to a variety of clients with a focus on the construction, manufacturing and architectural and engineering industries. Bob also specializes in auditing employee benefit plans, working with clients to help identify and resolve accounting issues, as well as discovering, investigating and resolving fraud cases. For more information on this topic, you may contact Bob at rreeves@dmcpas.com or (518) 836-5661.