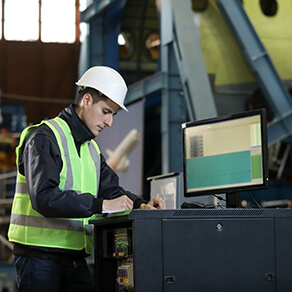
The Evolution of ERP to Today’s Modern Business Systems
For many manufacturing companies in the late 1990s and early 2000s, the implementation of an Enterprise Resource Planning (ERP) system promised greater efficiency and effectiveness for their operations under a single solution business system. Many managers hoped to achieve what the highly respected management consultant, author and educator Peter Drucker characterized as the “one management” concept for production.
As ERP grew in popularity, it became evident that its benefits could only be achieved by those manufacturers that could afford the high cost of sophisticated software as well as implement successful change management within their organizations. When the implementation of several large-scale SAP and Oracle systems fell short of success, companies realized that their management teams often misunderstood the risks associated with large-scale business change. Business continuity was believed to be the top risk to achieving a successful ERP implementation project. However, the failure to effectively manage organizational change was more often the case.
Manufacturers today have access to a broad range of modern business systems tailored to specific industry needs. These systems, properly implemented, provide a consistent and reliable foundation for operations, significantly enhancing decision-making, streamlining production and bringing Drucker’s unified management vision closer to reality.
Advantages of Integrated Business Systems
Modern ERP platforms are now highly modular, scalable and cloud-native, built on advanced frameworks that support interoperability across business functions. Platforms like NetSuite, Acumatica and Microsoft Dynamics 365 remain strong players, while newer AI-enhanced systems and industry-specific ERP providers continue to gain traction.
These advancements have been fueled by the rise of open-source development and enterprise-grade technologies pioneered by leaders like Microsoft, Google and Amazon Web Services. These companies made their toolsets freely available to the open-source community and many business system software publishers rebuilt the front end of their platforms using these new, highly flexible software development frameworks and available software libraries.
As of 2025, tools incorporating artificial intelligence, predictive analytics and machine learning have become core features of competitive ERP systems, enabling real-time insights and proactive decision-making.
With these integrated systems, manufacturers are better equipped to respond to changing business conditions, streamline value chain efficiency, align operations with sales, improve product quality and, most importantly, exceed evolving customer expectations. They also empower organizations to implement performance-based compensation plans linked to up-to-date, cross-functional key performance indicators (KPIs) across company functions.
Winning Organizations Adapt to Gain Substantial Benefit
Despite the widespread availability of modern tools, some small and mid-sized manufacturers still lag in adopting integrated business systems. The issue often isn’t the technology itself, but the leadership’s unwillingness to evolve. Many continue relying on outdated applications or unsupported customized systems to manage their businesses. Their reluctance to invest in new business systems severely limits their ability to improve operations, pose cybersecurity risks and hinder scalability.
Some management teams fail to adapt and gain the benefits of integrated business systems because they do not view technology as a core element in their strategic planning process. They may operate in a business-as-usual mindset built on a loyal customer base with little consideration for margin compression over time and customer-centric product innovation.
To compete effectively in a global, fast-paced business landscape, manufacturers must embrace the most current technologies. By investing in modern ERP solutions that support industry best practices and AI-driven automation, they position themselves not just to survive, but to lead.
Being successful in manufacturing means more than efficient operations. It means fostering a culture that values innovation, agility and long-term strategic thinking. Embracing the right technology is no longer optional, it’s essential for future growth and sustained market leadership. Contact us with questions.