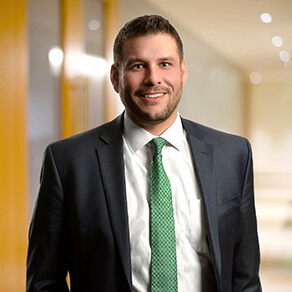
How to Leverage Inventory Cost Management to Improve Your Company’s Profitability
For many companies, especially manufacturing firms, balancing inventory costs is vital to your company’s success, but it can also be a guessing game that is difficult to predict. Playing a vital role in successfully managing growth from your business strategy, inventory cost management requires an effective system to sustain.
With an overall effective inventory management system in your company, it’s much easier to capture the appropriate costs, to include your overhead expenses, so that you’re able to implement sales and pricing strategies that improve your company’s profitability and growth.
Finding a Balance in Inventory and Sales
Much like your checking account balance, your inventory is considered to be an asset on your company’s balance sheet. However, inventory can also become a liability because it doesn’t always have outstanding liquidity. With too much inventory on hand in your warehouse, you’ll have reduced purchasing flexibility, including when you want to adapt to market demand shifts, keep ahead of your competition, increase business profitability, or purchase and use new or better products. On the opposite side, maintaining insufficient inventory can lead to supply chain issues, customer dissatisfaction, loss of customers and lowered profitability. For this reason, it’s of vital importance that manufacturers create a balance between what will sell and what’s on hand to create new products to replace sold units.
Inventory Data Collection
Collecting data from both your current stock and inventory expenses as well as supply chain and market demand is vital if you want to leverage your inventory cost management process to the max. It’s for that reason that understanding what those insights mean will help you develop better business strategies and make improved company decisions.
Start by analyzing the data on your existing stock. This prevents you from accumulating carrying costs that are associated with obsolescence while making it easier for you to manage your storage and materials handling expenses, which are usually tied to your warehousing and moving of your inventory. Understanding the details regarding what stock you have on hand also helps you avoid fraud and theft issues. When you analyze sales data, you can better align your inventory with the current demand in the market. This ensures that you’re able to meet your customers’ demands by providing timely delivery of the goods and services you create while avoiding overextending your costs.
By performing regular assessments of your vendors, you’ll be able to gain insights to avoid potential supply chain issues, place orders in a timely manner and avoid possible shortages. Additionally, in conjunction with your inventory expense data, the information that you gather makes it easier to forecast future cost, produce more accurate revenue projections and track your company’s performance in these areas.
Inventory Data Analysis
There are several types of data analysis you can perform on your inventory, but we’d like to focus on a couple that are used by the vast majority of manufacturers:
-
- Margin Analysis allows manufacturers to determine each product’s margins by compiling all the associated product costs and then subtracting those expenses from the revenue the product generates. By comparing actual supplies, labor, and overhead expenses against the budget estimates, variance analysis can be used by the manufacturers so that the cause behind any discrepancies can be discovered.
- ABC Analysis makes it easier to reduce excess, prioritize items impacting inventory cost and manage shortages. The analysis is calculated by multiplying the cost per unit by the number sold annually to determine annual usage value. Then, calculate cumulative products sold percentage versus the annual consumption value. This allows you to categorize inventory based on data:
-
- “A” represents the smallest category with your highest valued products accounting for the bulk of your revenue, usually 80%.
- “B” is the middle-of-the-road category, with products of moderate value and revenue generation, usually 15%.
- “C” is the largest products by volume that generate the least total revenue, usually 5%.
-
Because each manufacturer is different, you’ll see shifts. Inventory needs may be different between locations. The analysis may need to be disaggregated by location or similar factors. The 80/20 rule is the primary principle in ABC Analysis, where 80% of the total output will be generated by 20% of your input. Prioritizing products in your “A” group will allow you to focus your strategy on the smallest number of products to generate the largest return. This is why ABC Analysis can help you keep the right products in stock to meet demand while eliminating excess inventory and managing expenses.
Adding Inventory to Your Tax and Accounting Strategy
As part of your overall tax and accounting strategy, how you manage your inventory can have a significant impact on your total tax liability at the end of the fiscal year. Contact us. We have specialists in the manufacturing sector who can help you get to know what your options are so that you can leverage any opportunities that come your way, allowing you to avoid risk, increase profitability and improve operations.
Contributing author: Benjamin A. Sumner, CPA, is an audit partner with over 15 years of experience providing auditing, accounting and advisory services to a wide variety of privately-held businesses. For more information on this topic, contact Ben at bsumner@dmcpas.com or (315) 472-9127.